
ReplicatorG contains as its first example this calibration box: look under the Examples section of the File menu.
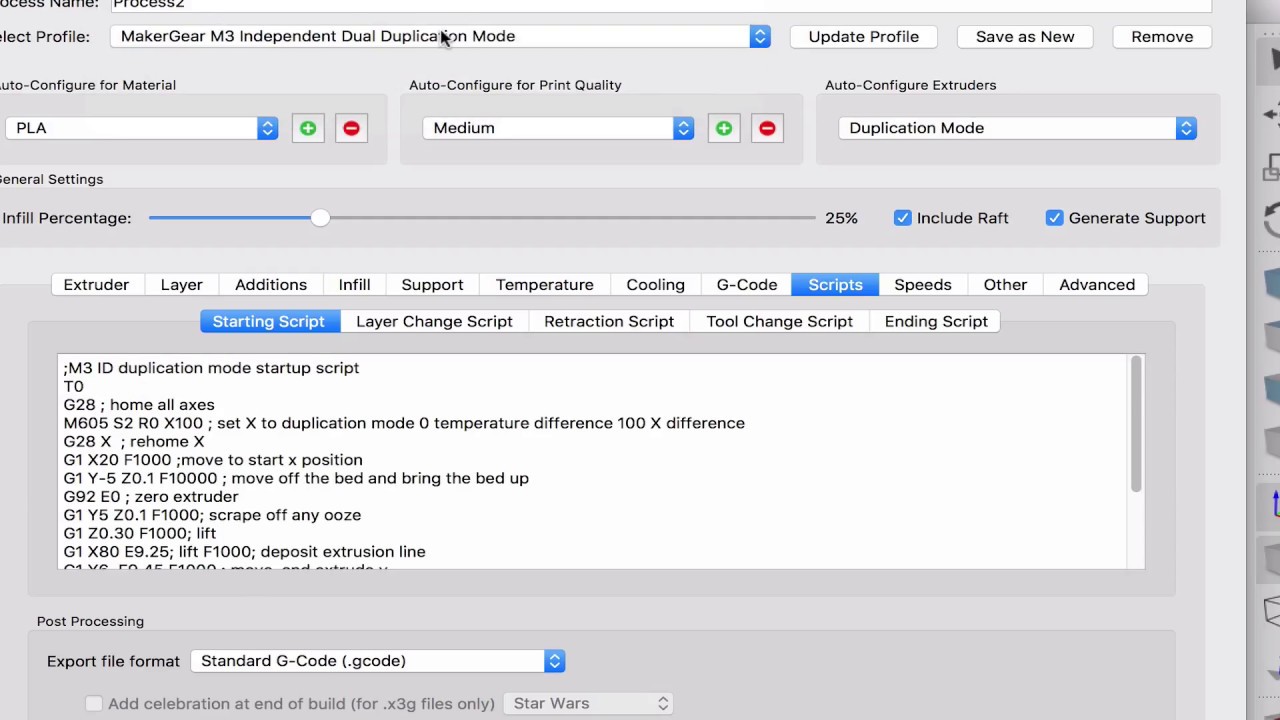
Obtain a model for a 10 mm high box which is 20 mm on a side. Here is the step-by-step procedure for accomplishing this calibration:ġ. So, until you can print a good calibration box, there is little point in worrying about other printing defects you may be experiencing. Producing a respectable box involves calibrating a slicing profile to your printer and choice of filaments. In v1.To achieve quality prints, start by ensuring that you can print a decent calibration “box” whose top is nice and flat. In v1, if K was set to a high value which couldn’t be handled by your printer, then the printer was losing steps and/or using all of it’s processing power to execute extruder steps. LIN_ADVANCE can reduce your print acceleration While old v1 K values for PLA might be between 30-130, you can now expect K to be around 0.1-2.0. This smooth extruder operation and respecting of jerk limits ensures no extruder steps are skipped.Īs the unit of K has changed, you have to redo the K calibration procedure.The pressure adjustment moves don’t lead to a rattling extruder as it was in v1.0: as the extruder is now running at a smooth speed instead of jerking between multiples of extruder print speed.If the pressure corrections require faster adjustments than allowed by extruder jerk limit, the acceleration for this print move is limited to a value which allows to use extruder jerk speed as the upper limit. LIN_ADVANCE now respects hardware limitations set in Configuration.h, namely extruder jerk.Instead, the extruder runs at a fixed speed offset during pressure adjustment. Load inside stepper ISR reduced as no calculations are needed there any more.K is now a meaningful value with the unit or.No need for high acceleration and jerk values to get sharp edges.Visible and tangible print quality is increased even at lower printing speeds.Higher printing speeds are possible without any loss of print quality - as long as your extruder can handle the needed speed changes.Better dimensional precision due to reduced bleeding edges.
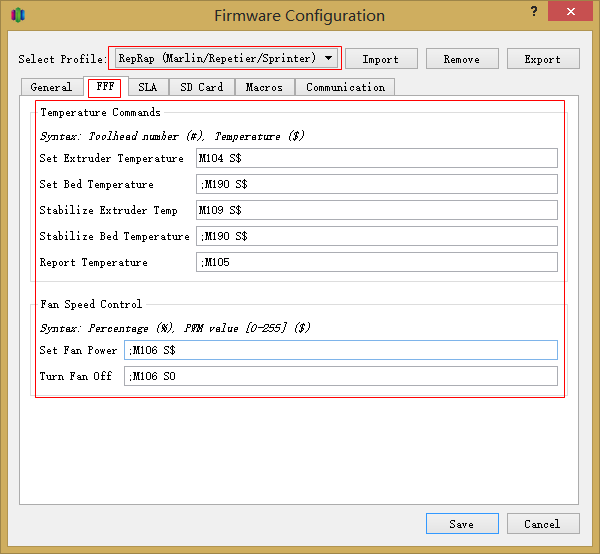
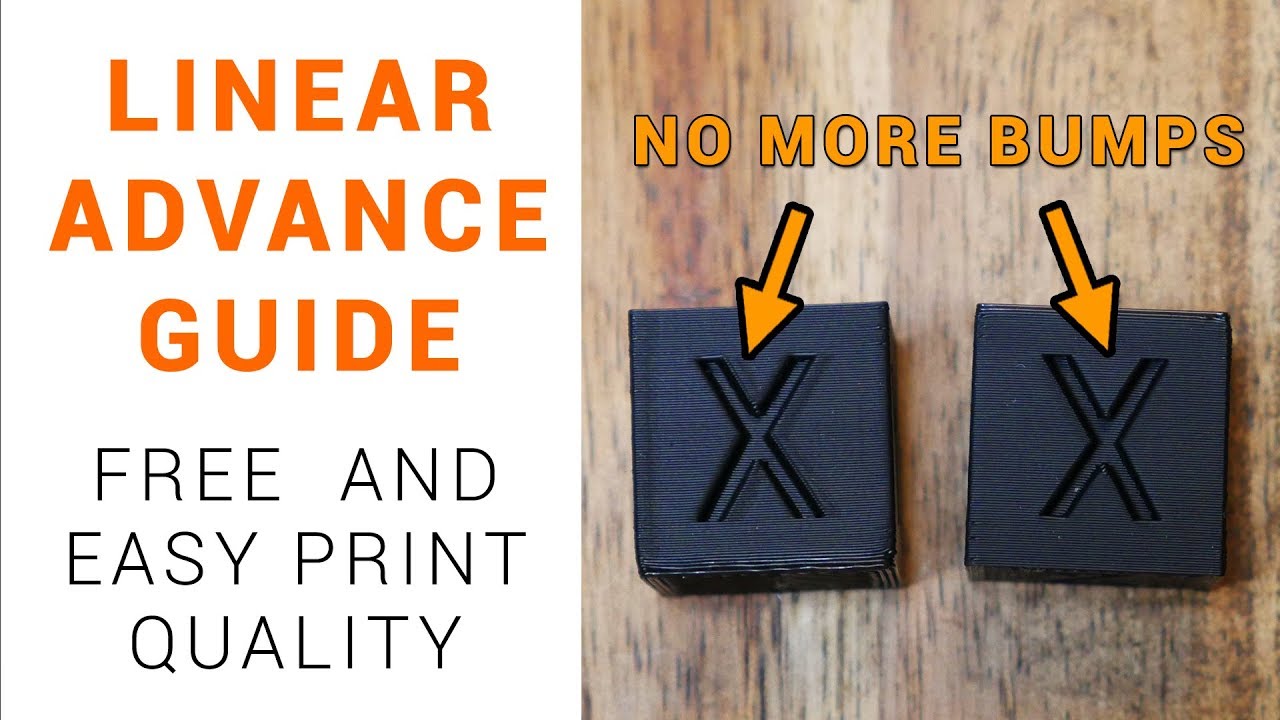
Once Linear Advance is properly tuned, bleeding edges and rough solid infill should be nearly eliminated. Since the root cause is pressure, LIN_ADVANCE de-couples extrusion from the other axes to produce the correct pressure inside the nozzle, adapting to the printing speed. Some slicers include an option to end extrusion early in each move, but this adds more complexity to the G-code and has to be retuned for different temperatures and materials. Tuning the flow can help, but this may lead to under-extrusion when starting new lines. These problems are minor or even imperceptible at low printing speeds, but they become more noticeable and problematic as print speeds increase. The top solid infill displays roughness where the print direction changes on perimeters. Even with the best tuning the corners are usually not sharp, but bleed out. But an extruder is not a linear system, so this approach leads, most obviously, to extra material being extruded at the end of each linear movement. The extruder motor moves in linear proportion to all the other motors, maintaining exactly the same acceleration profile and start/stop points. Under default conditions, extruder axis movement is treated in the same way as the XYZ linear axes.
